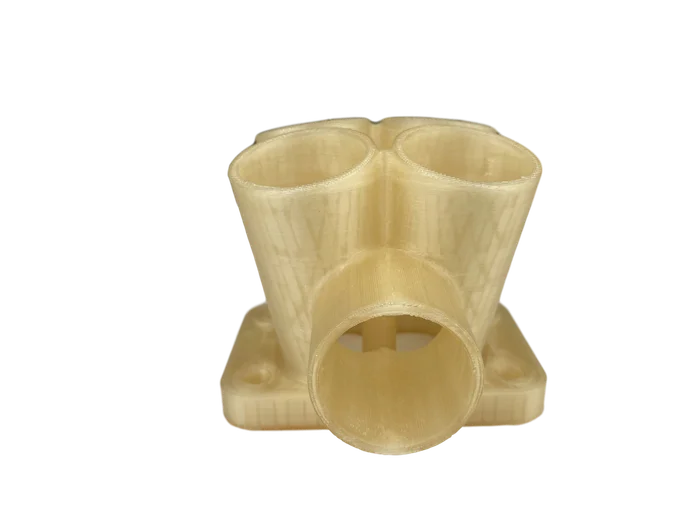
Strategies to tackle warping in high-temperature 3D printing: Unleashing the power of infill patterns
In the realm of high-temperature 3D printing, where durability and heat resistance are paramount, warping can be a pesky adversary that threatens the quality of our printed creations. But fear not! We shall embark on a journey to explore a potent strategy to combat warping: the ingenious utilization of diverse infill patterns. Delving into the technical details, we will unravel the secrets behind different infill patterns and their potential to mitigate warping. Brace yourself for an enlightening expedition through the realms of stress and geometry!
Understanding Infill Patterns
Infill patterns play a crucial role in providing structural support and strength to 3D printed objects. They consist of a lattice-like structure that fills the internal regions of the object, providing stability and reducing material usage. The choice of infill pattern can significantly impact the warping behavior of high-temperature materials.
The Influence of Infill Patterns on Warping
The selection of an appropriate infill pattern is vital for mitigating warping in high-temperature 3D printing. Different infill patterns exhibit distinct characteristics and stress distribution properties that can either exacerbate or alleviate warping tendencies.
Straight Line Infill Patterns
Infill patterns characterized by long straight lines, such as the rectilinear or grid patterns, are commonly used in 3D printing. While these patterns offer good structural support, they can intensify warping due to stress concentration along the straight lines. As high-temperature materials cool down, the contraction-induced stresses become localized along these lines, increasing the risk of warping.
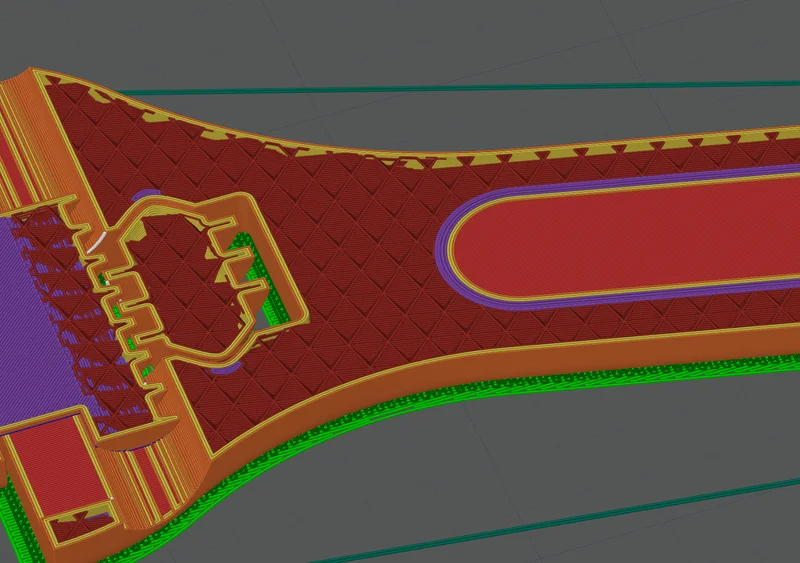
Cubic infill pattern
Curved Organic Infill Patterns
On the other hand, infill patterns with more curved and organic geometries, such as the honeycomb or gyroid patterns, offer potential solutions to mitigate warping. These patterns distribute stresses more evenly throughout the structure, minimizing the concentration of stress along specific lines. As a result, the risk of warping is significantly reduced, and the printed object can retain its dimensional stability even when subjected to high temperatures.
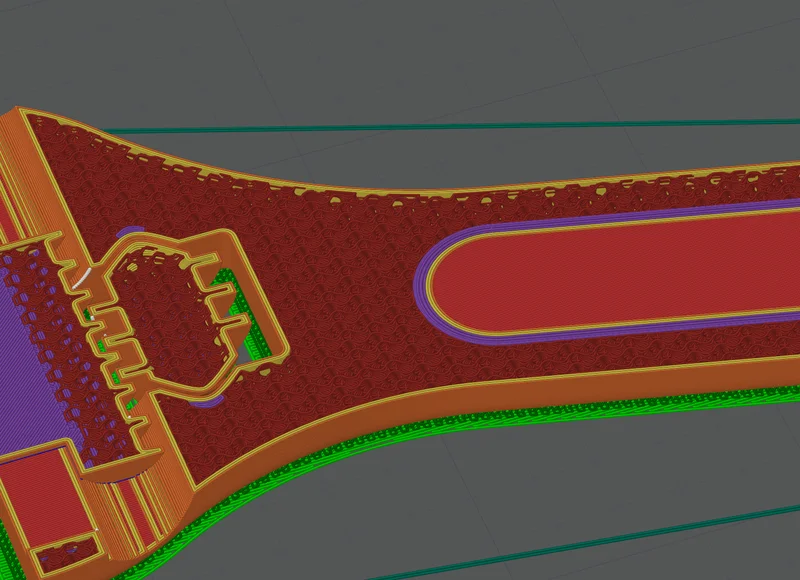
Gyroid infill pattern
Optimal Infill Pattern Selection
While each infill pattern has its advantages, the choice of the best pattern depends on various factors such as material properties, desired mechanical strength, and part geometry. For high-temperature materials like PEEK, infill patterns with curved and organic structures, such as the honeycomb pattern, often prove to be beneficial. The honeycomb pattern excels in stress dispersion and offers excellent stability, making it an ideal choice for mitigating warping in PEEK prints.
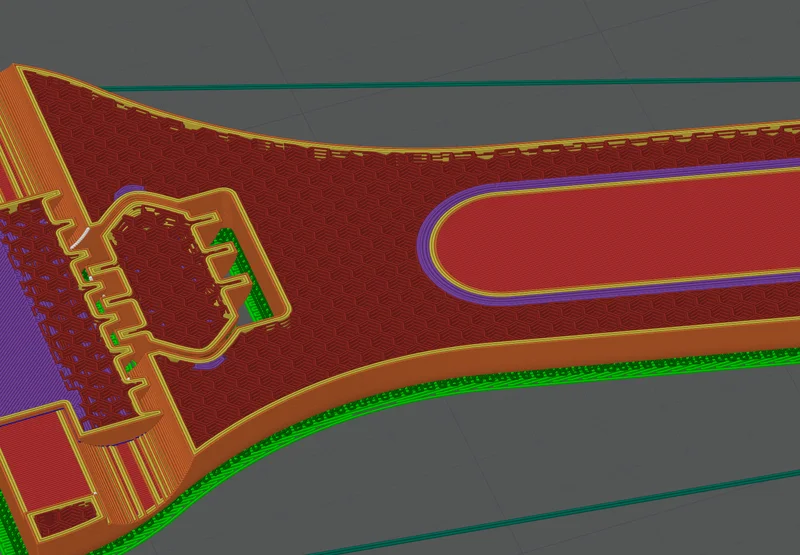
Honeycomb infill pattern
Balancing Strength and Warping Mitigation
When selecting an infill pattern, it is important to strike a balance between structural strength and warping mitigation. Infill patterns with long straight lines may provide greater strength but increase the risk of warping. Conversely, curved organic patterns reduce warping but may sacrifice some mechanical strength. Finding the optimal compromise is essential for achieving the desired print quality.
Experimental Approaches and Optimization
The choice of infill pattern should be informed by iterative testing and optimization. By experimenting with different infill patterns, including variations of the honeycomb pattern, one can identify the optimal configuration that minimizes warping while maintaining the required mechanical properties. Additionally, adjusting the infill density and pattern orientation can further enhance the warping mitigation capabilities of the chosen infill pattern.
Mitigating warping in high-temperature 3D printing is crucial for achieving successful prints with excellent dimensional accuracy. The use of different infill patterns, particularly those with curved and organic geometries like the honeycomb pattern, can help distribute stresses more uniformly and reduce the risk of warping.
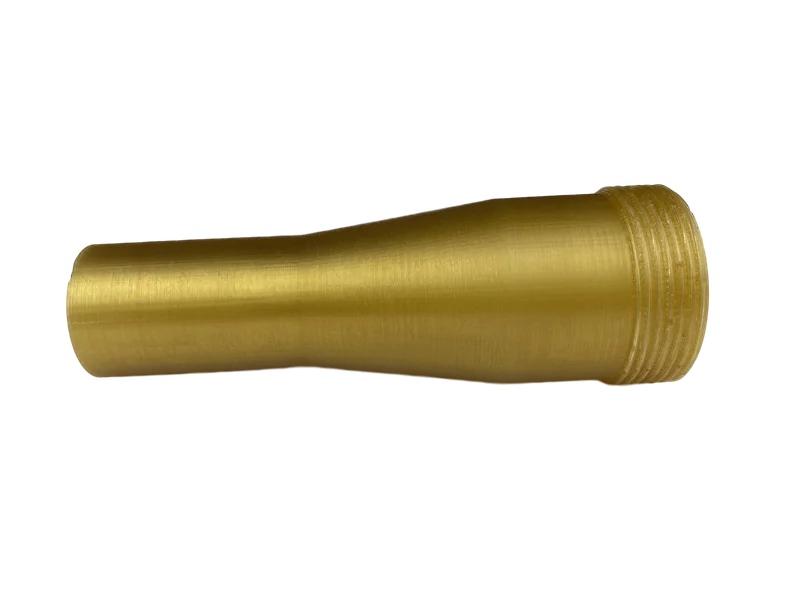
Ultem 1010 with circular infill
By understanding the relationship between infill patterns, stress distribution, and warping, subject matter experts can optimize their printing strategies and achieve superior results in high-temperature 3D printing applications. Through iterative testing, fine-tuning of infill density and pattern orientation, and thoughtful consideration of material properties, the optimal infill pattern can be selected to minimize warping while maintaining the desired mechanical strength and stability. With this knowledge in hand, practitioners can embark on their high-temperature printing journeys with confidence, delivering exceptional quality prints in the face of challenging materials like PEEK.
Add a Comment