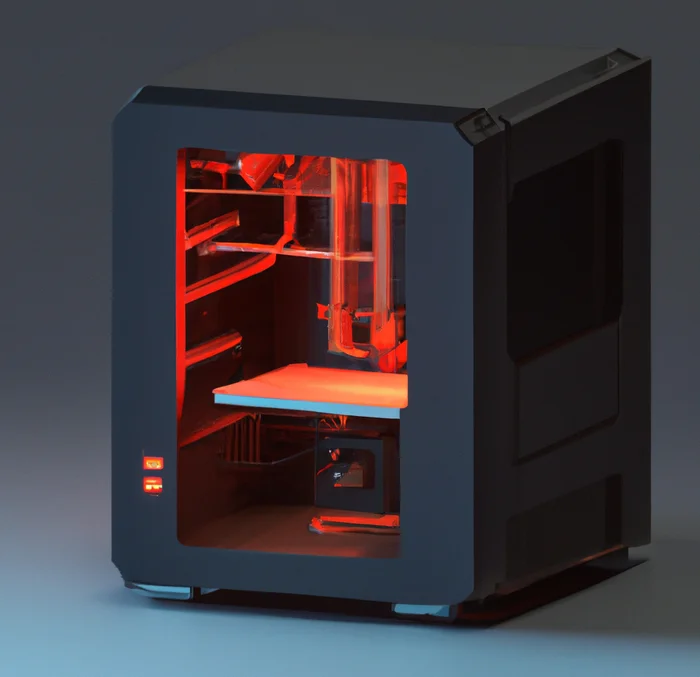
The crucial role of chamber temperature in printing high-performance materials
In the world of additive manufacturing, temperature control is a critical factor that directly impacts the quality and integrity of printed parts. This is particularly true when printing high-performance materials such as PEEK (Polyetheretherketone), PEI (Polyetherimide), and PPSU (Polyphenylsulfone). Achieving optimal chamber temperature during the printing process is of paramount importance to ensure successful layer bonding, prevent delamination, and minimize residual stresses in the final printed parts. In this article, we delve into the significance of chamber temperature and its impact on the print quality and mechanical properties of PEEK, PEI, and PPSU.
Layer Bonding: Ensuring Structural Integrity
Effective layer bonding is crucial to the structural integrity of printed parts. When printing with high-performance materials, maintaining a suitable chamber temperature is essential for promoting proper interlayer adhesion. These materials have relatively high glass transition temperatures (Tg), necessitating controlled thermal conditions to avoid premature cooling and subsequent weak interlayer bonds. Inadequate chamber temperatures can lead to insufficient heat transfer to the previously printed layer, resulting in poor fusion between layers and reduced overall strength.
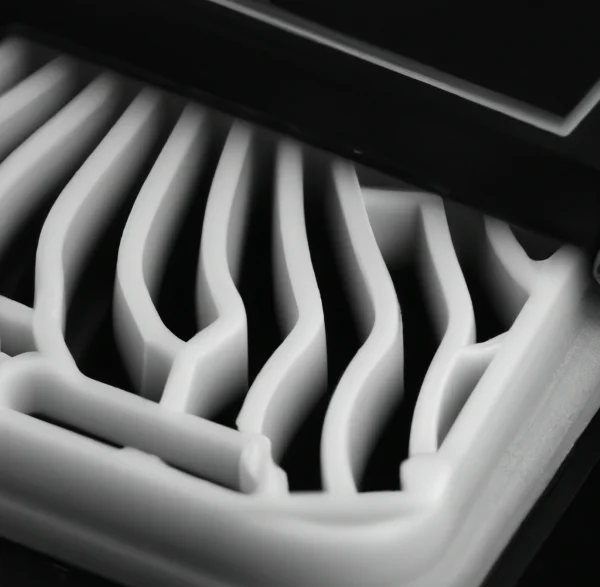
The Importance of a Hot Enough Previous Layer
To achieve optimal layer bonding, it is imperative that the previous layer remains at a sufficiently high temperature while the subsequent layer is being printed. The chamber temperature plays a significant role in preventing the previous layer from cooling too quickly. Rapid cooling can induce thermal gradients within the part, leading to interfacial stresses, delamination, and decreased mechanical performance. A consistently heated chamber helps to maintain the necessary temperature for the previous layer, ensuring proper melt flow and interlayer adhesion.
Minimizing Stresses for Better Part Quality
Inadequate chamber temperature can introduce significant stresses into printed parts. High-performance thermoplastics exhibit low coefficients of thermal expansion (CTE) and can experience substantial dimensional changes during the cooling process. If the chamber temperature is not appropriately controlled, thermal gradients within the part can cause differential cooling and lead to the development of residual stresses. These stresses can result in warping, distortion, and even part failure. Maintaining a uniform and elevated chamber temperature throughout the printing process helps to mitigate these thermal stresses, yielding parts with improved dimensional accuracy and mechanical properties.
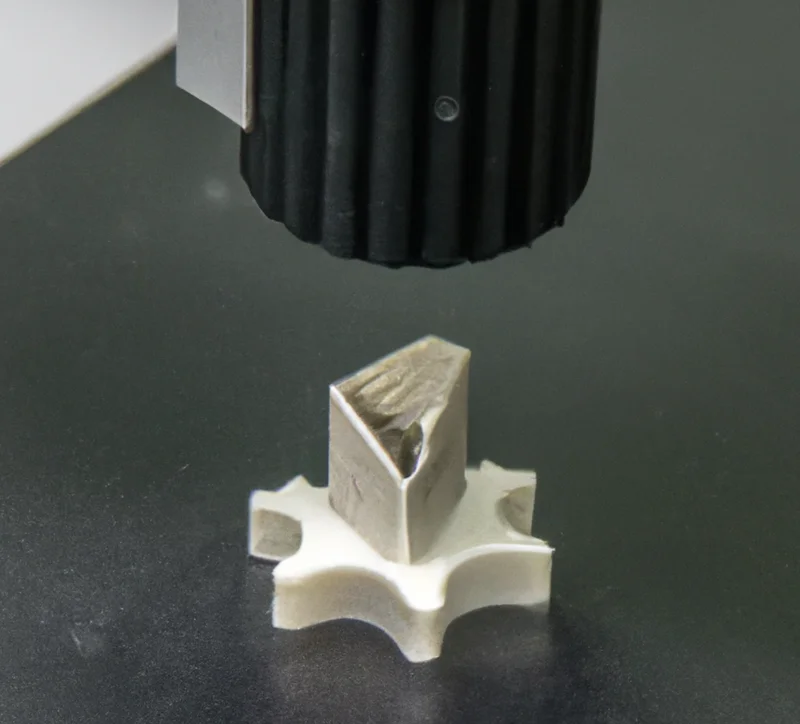
Influence on Mechanical Properties
Chamber temperature also plays a critical role in determining the final mechanical properties of printed parts. High-performance materials like PEEK, PEI, and PPSU are known for their exceptional strength, heat resistance, and chemical stability. However, these properties can be compromised if the chamber temperature is not optimized. Insufficient chamber temperature can result in incomplete fusion between layers, leading to weak interlayer bonds and reduced mechanical performance. Conversely, maintaining an adequate chamber temperature helps to maximize layer adhesion, resulting in parts with superior strength, toughness, and overall reliability.
The 3D Labs HTX and StarLab: Meeting Temperature Requirements
Printing high-performance materials like PEEK, PEI, and PPSU requires printers with precise chamber temperature control. That's where the 3D Labs HTX and StarLab come into play. These cutting-edge printers are designed specifically for printing with advanced thermoplastics, offering chamber temperatures of 100°C and 250°C, respectively.
The 3D Labs HTX provides a controlled environment with a chamber temperature of 100°C, allowing for optimal printing conditions of PEEK, PEI, and PPSU. With this printer, you can ensure the necessary interlayer adhesion, minimize thermal gradients, and reduce the risk of part distortion or delamination. The chamber temperature is carefully regulated to promote excellent layer bonding and produce high-quality, robust printed parts.
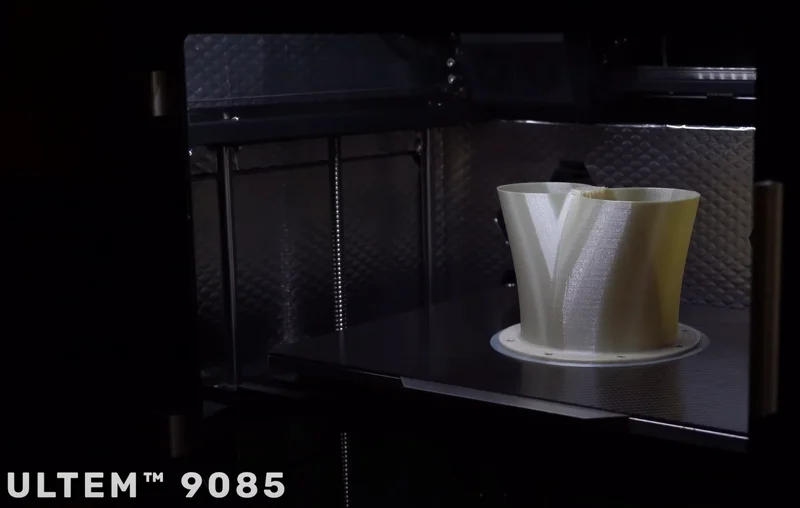
For applications that demand even higher chamber temperatures, the 3D Labs StarLab is the ideal choice. With a chamber temperature of 250°C, it offers an extended temperature range suitable for printing advanced materials such as PEEK, PEI, and PPSU with exceptional precision and reliability. The elevated chamber temperature ensures superior interlayer adhesion, minimizes residual stresses, and enables the production of parts with outstanding mechanical properties.
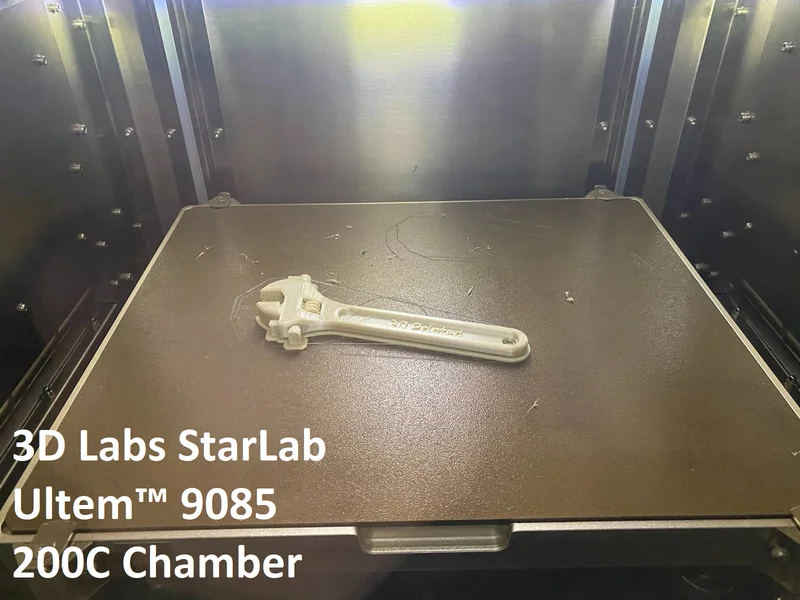
Both the 3D Labs HTX and StarLab feature advanced temperature control systems that maintain the desired chamber temperature throughout the printing process. This level of control allows you to confidently print high-performance materials without compromising their mechanical integrity.
The 3D Labs HTX and StarLab printers are equipped with state-of-the-art heating elements and insulation, ensuring precise and stable chamber temperatures. These printers are designed to provide a reliable and controlled printing environment, allowing you to harness the full potential of materials like PEEK, PEI, and PPSU.
By utilizing the 3D Labs HTX or StarLab, you can optimize the printing process for high-performance materials, reduce print failures, and achieve exceptional part quality. These printers offer the necessary temperature control to overcome the challenges associated with printing advanced thermoplastics, ultimately enabling you to unlock new possibilities in additive manufacturing.
Add a Comment